Duplex Stainless Steel Overview
Duplex Stainless Steels, also referred to as austenitic-ferritic stainless steels, are a family of grades with about equal proportions of ferrite and austenite. These steels have a duplex microstructure which contributes to their high strength and high resistance to stress corrosion cracking. Due to their high content of chromium, nitrogen and molybdenum, duplex steels offer good resistance to local and uniform corrosion. Duplex stainless steels have good weld ability.
Duplex stainless steels are called “duplex” because they have a two-phase microstructure consisting of grains of ferritic and austenitic stainless steel. The picture shows the yellow austenitic phase as “islands” surrounded by the blue ferritic phase. When duplex stainless steel is melted it solidifies from the liquid phase to a completely ferritic structure. As the material cools to room temperature, about half of the ferritic grains transform to austenitic grains (“islands”). The result is a microstructure of roughly 50% austenite and 50% ferrite.
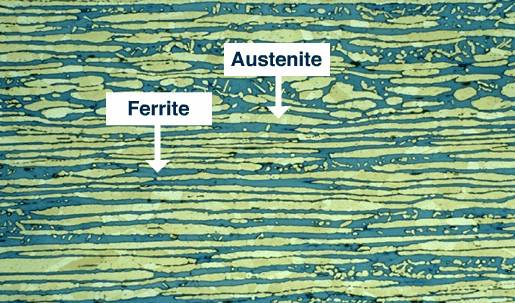
Duplex stainless steels have a two-phase microstructure of austenite and ferrite grains.
The duplex structure gives this family of stainless steels a combination of attractive properties:
Strength: Duplex stainless steels are about twice as strong as regular austenitic or ferritic stainless steels.
Toughness and ductility: Duplex stainless steels have significantly better toughness and ductility than ferritic grades; however, they do not reach the excellent values of austenitic grades.
Corrosion resistance: As with all stainless steels, corrosion resistance depends mostly on the composition of the stainless steel. For chloride pitting and crevice corrosion resistance, their chromium, molybdenum and nitrogen content are most important. Duplex stainless steel grades have a range of corrosion resistance, similar to the range for austenitic stainless steels, i.e from Type 304 or 316 (e.g. LDX 2101©) to 6% molybdenum (e.g. SAF 2507©) stainless steels.
Stress corrosion cracking resistance: Duplex stainless steels show very good stress corrosion cracking (SCC) resistance, a property they have “inherited” from the ferritic side. SCC can be a problem under certain circumstances (chlorides, humidity, elevated temperature) for standard austenitics such as Types 304 and 316.
Cost: Duplex stainless steels have lower nickel and molybdenum contents than their austenitic counterparts of similar corrosion resistance. Due to the lower alloying content, duplex stainless steels can be lower in cost, especially in times of high alloy surcharges. Additionally, it may often be possible to reduce the section thickness of duplex stainless steel, due to its increased yield strength compared to austenitic stainless steel. The combination can lead to significant cost and weight savings compared to a solution in austenitic stainless steels.
Today, modern duplex stainless steels can be divided into three groups:
- Lean Duplex such as LDX2101
- Standard Duplex such as 2205, the work-horse grade accounting for more than 80% of duplex usage
- Super Duplex such as Ferralium 255, Zeron 100 and 2507
Of the duplex grades, duplex 2205 is the most widely used. However, the super duplex steels like Zeron® 100 and 2507 are excellent for servicing severe corrosive environments, such as offshore and marine applications. Lean duplex 2101 is available as an economic alternative to 300 series stainless steels.
What are the Characteristics of Duplex Stainless Steels®?
- Very good resistance to uniform corrosion
- Very good resistance to pitting and crevice corrosion
- High resistance to stress corrosion cracking and corrosion fatigue
- High mechanical strength
- Good sulfide stress corrosion resistance
- Good abrasion and erosion resistance
- Good fatigue resistance high energy absorption
- Low thermal expansion
- Good weld ability
In what Applications are Duplex Stainless Steels® used?
- Oil and gas equipment
- Offshore technology
- Seawater desalination plants
- Chemical industry, especially when handling chlorides
- Flue-gas cleaning
- Desalination plants and seawater systems
- Pulp and paper industry
- Cargo tanks and pipe systems in chemical tankers
- Firewalls and blast walls on offshore platforms
- Bridges
- Storage tanks
- Pressure vessels, reactor tanks, and heat exchangers
- Rotors, impellers and shafts
Remark
- All Trademarks and/or Trade names are the properties of their respective owners!
- The materials comes from the internet, and all the copyrights belongs to the original organization and creator.
- The materials above just for reference, TaiWah will NOT responsible for all the problems and loss resulted from type and material selection
Disclaimer: The data and information here are believed to be reliable. However, this material is not intended as a substitute
for competent professional engineering assistance which is a requisite to any specific application. TaiWah , its
companies or businesses, makes no warranty and assumes no legal liability or responsibility for results to be obtained in any
particular situation, and shall not be liable for any direct, indirect, special or consequential damages therefore. This material
is subject to revision without prior notice.