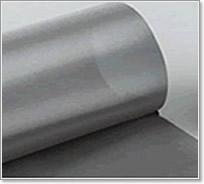
Materials: Typical materials of Hastelloy alloy wire mesh
HASTELLOY® Family of Corrosion-Resistant Alloys |
HASTELLOY® B-3® alloy |
Same excellent resistance to hydrochloric acid and other strongly reducing chemicals as B-2 alloy, but with significantly better thermal stability, fabricability and stress corrosion cracking resistance. |
HASTELLOY® C-4 alloy |
High-temperature stability in the 1200-1900°F (650-1040°C) range as evidenced by good ductility and corrosion resistance. Virtually the same corrosion resistance as alloy C-276. |
HASTELLOY® C-22® alloy |
Better overall corrosion resistance in oxidizing corrosives than C-4, C-276 and 625 alloys. Outstanding resistance to localized corrosion and excellent resistance to stress corrosion cracking. Best alloy to use as universal weld filler metal to resist cor |
HASTELLOY® C-276 alloy |
Versatile, corrosion resistant alloy. Very good resistance to reducing, and mildly oxidizing corrosives. Excellent stress corrosion cracking resistance with very good resistance to localized attack. |
HASTELLOY® C-2000® alloy |
Most versatile, corrosion resistant alloy with excellent resistance to uniform corrosion in oxidizing or re-ducing environments. Excellent resistance to stress corrosion cracking and superior resistance to localized corrosion as compared to C-276 alloy. |
HASTELLOY® G-30® alloy |
Many advantages over other metallic and non-metallic materials in handling phosphoric acid, sulfuric acid, nitric acid, fluoride environments and oxidizing acid mixtures. |
HASTELLOY® G-35® alloy |
Excellent resistance to corrosion in highly oxidizing media and acidic chloride environments. |
HASTELLOY® N alloy |
Good resistance to aging and embrittlement and good fabricability. It has excellent resistance to hot fluoride salts in the temperature range of 1300°F to 1600°F (705°C-870°C). |
HASTELLOY® Family of Heat-Resistant Alloys |
HASTELLOY® S alloy |
Excellent thermal stability, good thermal fatigue resistance, good oxidation-resistance & relatively low expansion characteristics. Used in low-stress gas turbine parts. Excellent dissimilar filler metal. |
HASTELLOY® W alloy |
Excellent for welding dissimilar high-temperature alloys. Used extensively in aircraft engine repair and maintenance. |
HASTELLOY® X alloy |
Very good balance of strength, oxidation-resistance & fabricability. Most widely used material for aircraft, marine and industrial gas turbine engine combustors and fabricated parts. |
Process
Weaving pattern:
1.Plain weave
2.Twill weave
Surface Finishing: NA
Key Properties:
The primary function of the Hastelloy super alloys is that of effective survival under high-temperature, high-stress service in a moderately to severely corrosive, and/or erosion prone environment where more common and less expensive iron-based alloys would fail, including the pressure vessels of some nuclear reactors, chemical reactors, and pipes and valves in chemical industry.
Typical Applications:
The Corrosion-Resistant HASTELLOY® alloys are widely used by the chemical processing industries. The need for reliable performance leads to their acceptance and growth in the areas of energy, health and environmental, oil and gas, pharmaceutical and flue gas desulfurization industries. The attributes of HASTELLOY® alloys include high resistance to uniform attack, outstanding localized corrosion resistance, excellent stress corrosion cracking resistance, and ease of welding and fabrication.
The aircraft gas turbine engine market has traditionally been the major user of HASTELLOY® and HAYNES® high-temperature alloys.
Specifications
2mesh/inch-500mesh/inch General;
We produce wire cloth in all kinds of forms. The weaving style is determined according to our customers’ specific requirements, such as the material, the wire diameter, the size of the mesh, width and length.
Wire mesh specifications of Hastelloy alloys